製造工程
①材料検査
入荷した段階でキズや変形等の異常がないか検査します。
②鋼板切断加工(4尺、8尺シャーリング)
1枚の定尺の板を必要サイズへカットします。
用途 | 定尺サイズの部品プレス加工板材をプレスする事で様々な形に成形、カットを行います。 |
---|---|
特徴 | サイズ/25t、45t、80t、160t |
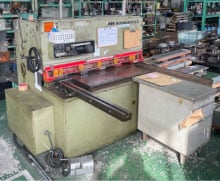
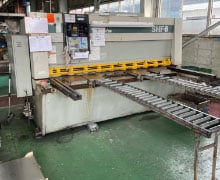
③鋼管切断加工(自動パイプ切断機)
1本の定尺パイプを必要サイズへ自動でカットします。
用途 | 定尺パイプのセットから切断まで行う自動機 |
---|---|
特徴 | ステンレス材対応可 Φ28.6~φ80対応可 |
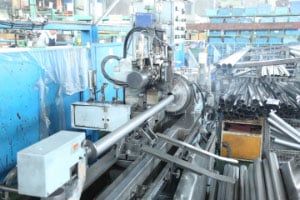
④部品プレス加工(25t、45t、80t、150tプレス機)
先程カットした板を数回にわけて、外皿・中皿・内筒部品へと成形していきます。
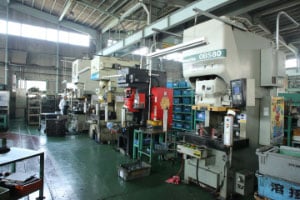
⑤鋼管曲げ加工(NCパイプベンダー)
先程カットしたパイプを設定されたデータに基づいて3次元に曲げていきます。
用途 | 規格データを基に一括でパイプの曲げ加工をする自動機 |
---|---|
特徴 | ステンレス材対応可 Φ28.6~φ80対応可 |
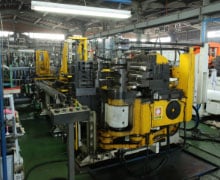
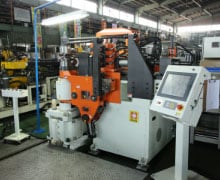
⑥外筒加工(ボディマルチ溶接機)
先程カットした板をマフラー本体サイズに合わして丸め、スポット溶接していきます。
用途 | 板材を丸め、スポット溶接を行い、フランジングまでを行う自動機 |
---|---|
特徴 | サイズ/φ75.0~φ275 |
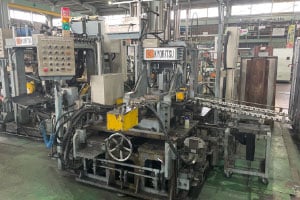
⑦内筒部品組み立て(CO2半自動溶接機)
先程加工した板やパイプを用いて本体内部の構造部分を組み付けていきます。
⑧フランジング加工(油圧圧入機)
先程丸めたマフラー本体をカシメル為にミミ出しを行います。
用途 | ボディマルチで加工できない特殊サイズの本体のフランジングを行います。 |
---|---|
特徴 | サイズ/φ130~2405 |
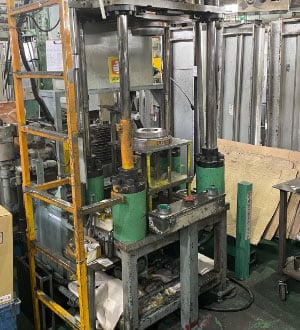
⑨パイプ先端加工(パイプ端末成形機、管端加工機)
先程曲げたパイプの先端を拡縮管や特殊加工(バルジ加工・スエージング加工・カール加工)を行います。
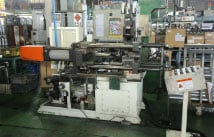

⑩本体部分の圧入(油圧圧入機)
マフラー本体の外筒に内筒を圧入し、組み込んでいきます。
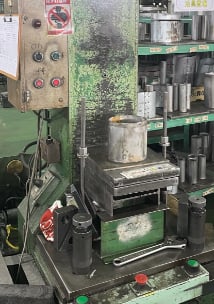
⑪外筒スポット溶接(スポット溶接機)
先程圧入した内筒を外筒にスポット溶接で溶接止めしていきます。
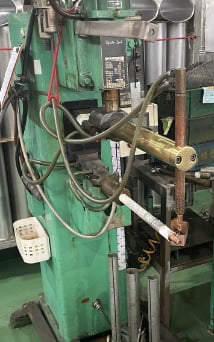
⑫巻締加工(シーマ)
マフラー本体と外皿をカシメ、蓋を閉めていきます。
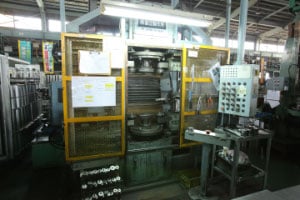
⑬部品組み付け(溶接ロボット、TIG溶接機)
パイプにフランジを溶接したり、金具にフックを溶接したり、小部品を製作していきます。
用途 | 各部品を溶接する自動機。 |
---|---|
特徴 | ティーチングデータを基にロボットが直接コントロールを行う自動溶接ロボット ステンレス材対応可 |
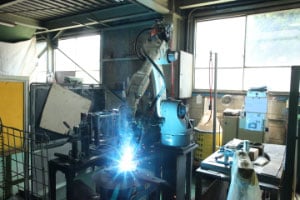
⑭溶接仕上げ加工(CO2半自動溶接機、TIG溶接機)
先程製作した小部品とマフラー本体を組付け溶接治具に乗せ、仮止め後、本付け溶接し製品を完成します。
⑮リーク検査
完成した製品全数にエアーを注入し、ピンホールや溶接穴などの溶接・部品不良の検査を行います。
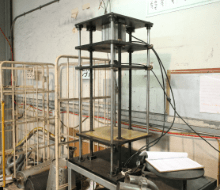
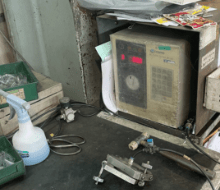
⑯塗装仕上げ
リーク検査に合格した製品は、耐熱塗料にて吹き付け塗装を行います。
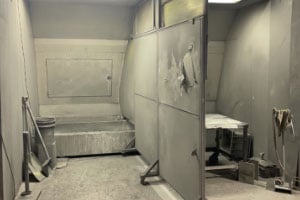
⑰包装ラベル貼付
塗装が乾いた商品には、一点一点梱包用の段ボールと付属品を貼付、完成です。
設備紹介
機械名称 | 種別 | 台数 |
---|---|---|
溶接ロボット | 溶接 | 4 |
CO2半自動溶接機 | 溶接 | 13 |
自動TIG溶接機 | 溶接 | 2 |
TIG溶接機 | 溶接 | 3 |
抵抗溶接機 | 溶接 | 3 |
3本ロール機 | 本体 | 2 |
ボディーマルチ | 本体 | 1 |
Wシーマ両端巻締め機 | 本体 | 1 |
片面巻締め機 | 本体 | 2 |
油圧圧入機 | 本体 | 7 |
油圧プレス10t | 本体 | 1 |
ウレタンロール機 | 本体 | 1 |
半自動グラスール巻きつけ機 | 本体 | 2 |
片面スポット溶接機 | 本体 | 1 |
4尺シャーリング | プレス | 1 |
8尺シャ-リング | プレス | 1 |
25tプレス | プレス | 1 |
45tプレス | プレス | 3 |
80tプレス | プレス | 2 |
150tプレス | プレス | 2 |
プレス(エアー式) | プレス | 1 |
レベラフィーダ・アンコイラ | プレス | 1 |
丸棒曲げ機 | プレス | 1 |
洗浄機 | プレス | 1 |
プレスブレーキ | プレス | 1 |
NCパイプベンダー | パイプ | 3 |
プレスベンダー | パイプ | 1 |
パイプ端末成形機 | パイプ | 2 |
管端加工機 | パイプ | 2 |
カルテンバッハ切断機 | パイプ | 1 |
自動パイプカッター | パイプ | 1 |
丸鋸カッター | パイプ | 1 |
丸鋸切断機 | パイプ | 1 |
縦型スリーブ機 | パイプ | 1 |
局所排気装置 | 仕上げ | 1 |
コンターマシン | 開発 | 2 |
セーパー | 開発 | 1 |
旋盤 | 開発 | 2 |
鋸盤 | 開発 | 1 |
フライス盤 | 開発 | 2 |
プラズマ切断機 | 開発 | 1 |
平面研削盤 | 開発 | 2 |
ボール盤 | 開発 | 5 |
ラジアルボール盤 | 開発 | 1 |
両頭グラインダー | 開発 | 1 |